Sorry for no post lately I went on a great vacation with my family for 8 days. Anyway this post is a three day roll up of yet more turtledeck fabrication. I started off wednesday night (11jan12) by laying in some tape at the aft bulk head to mask the line so I could lay up a couple of tapes for the turtle deck flange. I also cut the straight line on the turtle deck tails so that they could be re-glued straight as to not chaffe the fabric so the plans say. After I masked the turtle deck side I laid up 3 layers of 5.8 oz 282 carbon fiber. I also clamped and taped the cut lines back together with 2 layers of 282.
The next day (thursday 12Jan12) I marked the cut line on the out side of the turtle deck and cut the mask line using my dremel tool being careful not to cut into the new flange. This worked ok, not quite as smooth of a line as I wanted but it worked good enough. I also worked on ideas for the forward mold.
Saturday (14jan12) I decided to work on the mold for the forward bulkhead. I used my mold cut out blank and taped up the edges then I cut the same shape out of 0.016 2024-T3 I had laying around. I used the sheet metal because it gives a nice and perfect glossy finish. I then used my mid bulk head blank and trimmed it also radius the corners for to complete the “hole” space. and finally I used a block of wood that I taped with packing tape so that it wouldn’t stick. This one was a bit trickier since it had to be set at an angle and then screwed down into the wood of the cut out. I sandwiched everything together with dry wall screws and ratchet strapped in place which can be a big pain in the ass because of the angles/tapers of everything. I finally got it sitting in there nice and neat and laid up 3 layers of 5.8 oz 282 carbon graphite bi-weave into the mold.
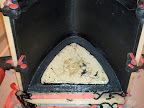
Sunday (15Jan12) I removed the mold and I was pleasantly surprised to find a perfectly molded beautiful forward bulk head. I trimmed it up and sanded the corners to a nice smooth radius. It fit well. I threw my canopy up on the fuselage to see how it fit and it fit well but then I noticed that I will be making a new canopy sheet metal since I tilt the turtle deck aft the metal no longer is long enough (see below picture) oh well, I’m replacing everything else might as well replace that too. I then spent most of the day building the mold for the aft bulkhead. This was done similarly to the forward bulkhead but instead of wood for the center piece I used a old plastic tub that just happened to be the right diameter. I again used sheet metal and tape for mold release. This time I laid up 4 layers since this one would be supporting fabric tension. The flange will be now 7 layers thick so nice and stiff hopefully. I spent the rest of my time cleaning up and playing around with the elevator trim cable since it came in the other day.
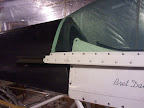
Time spent over 3 days: 20 hours
Total time spent: 1044 hours